From Prototype to Production: The Remarkable Journey of 3D Printing
The technology that powers our custom 3D printed skins and accessories has come a long way since its inception. In this article, we'll explore the fascinating evolution of 3D printing, from its humble beginnings to the sophisticated technology that enables personalized tech accessories today.
The Early Days: 1980s to 1990s
3D printing technology, originally known as "rapid prototyping," first emerged in the early 1980s. The first patent for stereolithography (SLA) was filed in 1984 by Charles Hull, who would later found 3D Systems, one of the industry's pioneering companies. Hull's invention used ultraviolet light to cure and solidify liquid polymer layer by layer, creating three-dimensional objects from digital designs.
This early technology was primarily used for industrial prototyping, allowing manufacturers to create test models of new products without the expense and time requirements of traditional manufacturing methods. However, these early machines were enormous, extremely expensive, and limited in their capabilities.
Did you know? The first 3D printer created by Charles Hull in 1984 used a process called stereolithography (SLA), which is still used today, though in much more refined forms.
Throughout the 1990s, additional 3D printing technologies emerged, including Fused Deposition Modeling (FDM), which extrudes heated thermoplastic material layer by layer, and Selective Laser Sintering (SLS), which uses lasers to fuse powdered materials into solid structures. These technologies expanded the range of materials that could be used in 3D printing, from basic plastics to more durable nylons and even some metals.
The Open-Source Revolution: 2000s
A significant turning point in 3D printing history came in 2005 with the launch of the RepRap (Replicating Rapid Prototyper) Project by Dr. Adrian Bowyer. This open-source initiative aimed to create self-replicating 3D printers that could produce most of their own components. The project democratized 3D printing technology, making it more accessible to hobbyists, small businesses, and educational institutions.
The impact of the RepRap Project cannot be overstated. By opening up the technology through open-source designs, the cost of 3D printers plummeted from tens of thousands of dollars to just a few hundred. This accessibility sparked innovation across the field, as more people could experiment with and improve upon existing designs.
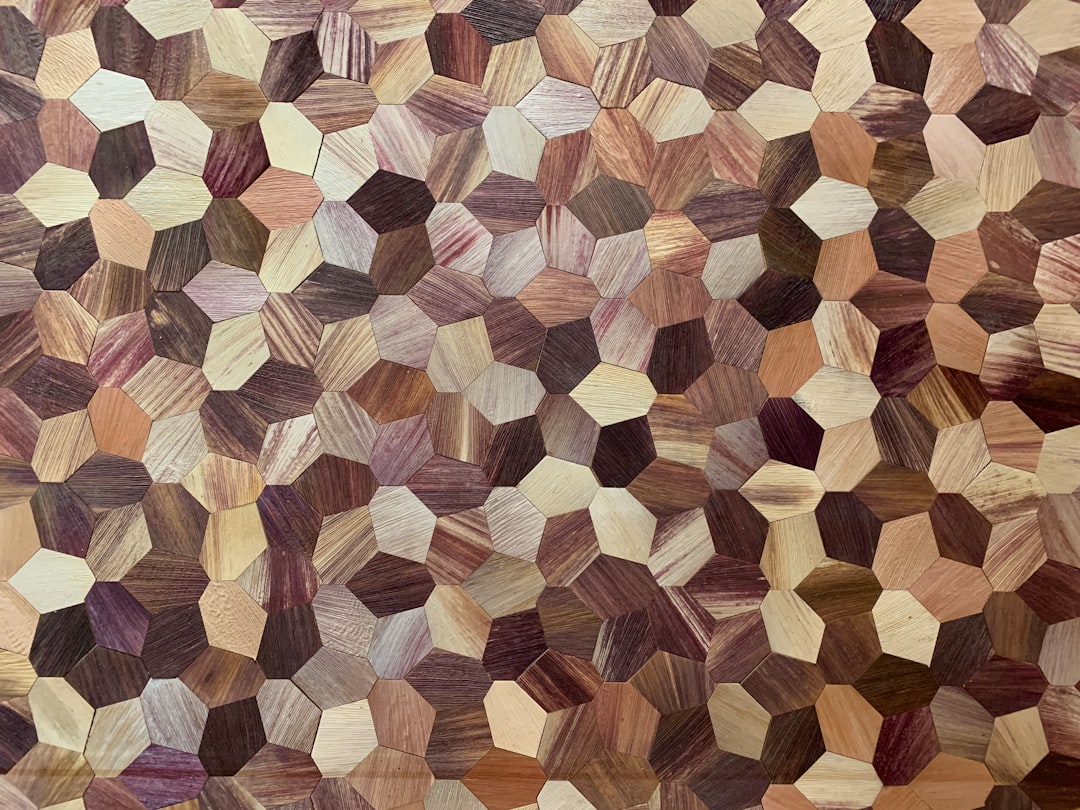
Mainstream Adoption: 2010s
By the early 2010s, 3D printing began to capture public imagination. Consumer-oriented 3D printers became available, and the media frequently featured stories about the technology's potential to revolutionize manufacturing. Companies like MakerBot and Ultimaker brought user-friendly 3D printers to market, while online services like Shapeways allowed people to order custom 3D printed items without owning a printer themselves.
During this period, 3D printing applications expanded dramatically beyond simple prototyping. The technology found uses in:
- Medical fields (custom prosthetics, anatomical models for surgery planning)
- Aerospace (lightweight components with complex geometries)
- Automotive manufacturing (custom parts and rapid prototyping)
- Fashion (experimental designs and customized accessories)
- Consumer products (personalized phone cases, jewelry, and other accessories)
Materials science also advanced significantly during this period. New filaments and printing materials emerged, including flexible materials, wood and metal composites, and even conductive materials that could carry electrical currents.
The Current State: Precision, Speed, and Customization
Today's 3D printing technology represents the culmination of decades of innovation. Modern printers offer unprecedented precision, with some capable of printing details as small as 25 microns (about half the width of a human hair). Print speeds have increased dramatically, and multi-material printing allows for complex objects with varying properties to be created in a single print job.
For custom tech accessories like the ones we create at FarmNSkirns, these advancements mean we can offer:
- Extremely precise fits for specific device models
- Complex textures and patterns that would be impossible with traditional manufacturing
- Combinations of materials in a single product (e.g., rigid structures with flexible elements)
- Fully customized designs that reflect individual style preferences
- Small-batch production without the high costs associated with traditional manufacturing methods
At FarmNSkirns, we use cutting-edge 3D printing technology to create custom skins and accessories that are precisely fitted to your devices while expressing your unique style.
The Future of 3D Printing in Personalization
Looking ahead, several emerging trends promise to further revolutionize 3D printing's role in creating personalized tech accessories:
Advanced Materials
Research into new printable materials continues at a rapid pace. We anticipate seeing more environmentally friendly options, ultra-durable composites, and materials with special properties like enhanced heat resistance or improved tactile qualities. These advancements will allow for even more versatile and functional custom accessories.
AI-Assisted Design
Artificial intelligence is beginning to play a role in 3D design, helping to optimize structures for both aesthetics and functionality. AI can suggest design improvements, generate pattern variations based on preferences, and even help ensure that designs will print successfully.
Faster, More Efficient Printing
New technologies like Continuous Liquid Interface Production (CLIP) and High-Speed Sintering (HSS) promise to dramatically reduce printing times while maintaining or improving quality. This will make custom production even more accessible and affordable.
Integration with Other Technologies
The combination of 3D printing with other technologies, such as embedded electronics or augmented reality previews, will create new possibilities for functional personalization. Imagine custom phone cases with built-in customized circuit patterns, or being able to preview exactly how a custom accessory will look on your device through AR before ordering.
Conclusion
The evolution of 3D printing from expensive industrial prototyping to accessible personalization technology represents one of the most significant manufacturing revolutions in recent history. At FarmNSkirns, we're proud to be part of this technological journey, harnessing the power of modern 3D printing to create unique, personalized tech accessories that weren't possible just a few years ago.
As the technology continues to advance, the possibilities for customization will only expand, allowing for ever more creative and functional expressions of personal style through technology accessories. We're excited to be at the forefront of this revolution, bringing the benefits of cutting-edge 3D printing directly to our customers.